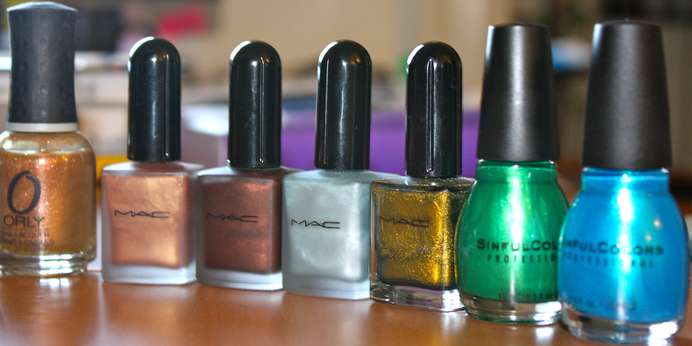
“C’mon, Lillian, just pick one,” says Jim. “It doesn’t really matter. We shouldn’t need to spend a half an hour in Walgreens every time.” Lillian, ignoring him, continues to scrutinize a bottle of metallic blue nail polish and a bottle of alloy blue nail polish, her face twisted in concentration. Jim looks at his watch. He’s already missed kick-off. “Lillian, c’mon,” he says. “They’re both blue.” Lillian clenches her fists around the bottle. “Da-ad!” she wails. “No, they’re NOT! You don’t understand!”
What Jim doesn’t understand, nail polish manufacturers do1: they’re not the same color. With designers large and small ordering mixes of anywhere from a dozen to some hundreds of different colors every year, it’s important for manufacturers to be able to distinguish and reliably produce minute differences in the shading, gloss, and lustre of nail polish. If Jim’s eyes can’t tell the difference, designers can. And manufacturers unable to do so stand to lose a lot more than missing the first quarter; batches that fail color standards cause lost production time and a waste of materials that can’t be reused. That’s why careful spectrophotometric measurement is an essential part of a nail polish manufacturer’s process.
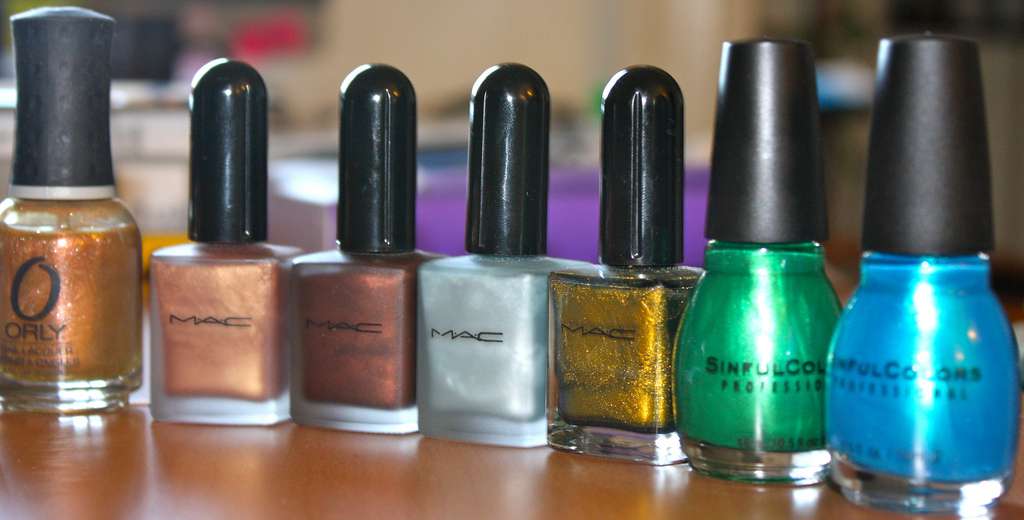
Metallic shades differ in luster and gloss. Image Credit: Flickr User Justiff Jones. (CC BY 2.0)